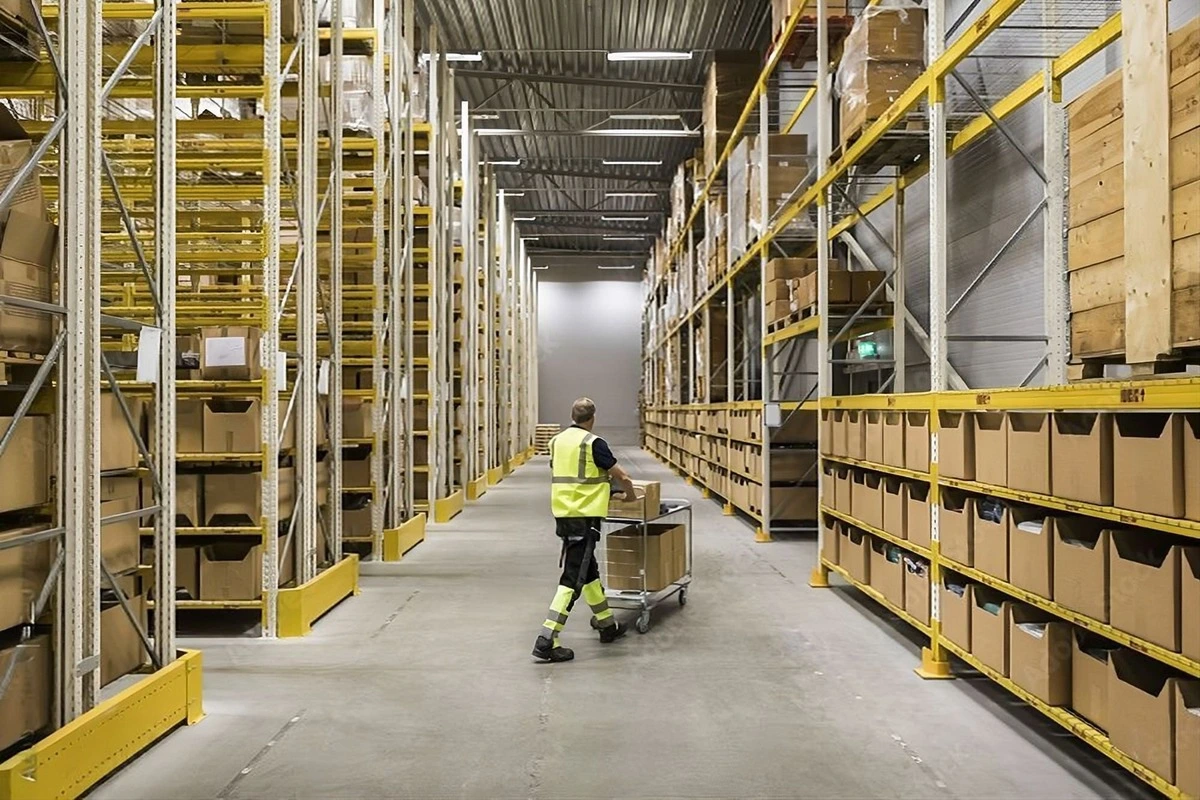
Warehouse Location Strategy: Finding the Sweet Spot for Efficiency
Warehousing is the backbone of a successful supply chain. The location of your warehouse can significantly impact various aspects of your business, from transportation costs to order fulfillment efficiency. In this article, we will explore the multifaceted aspects of Warehouse Location Strategies.
The Significance of Warehouse Location
Your warehouse’s location isn’t merely a point on a map; it’s a strategic decision that influences your bottom line. Let’s break down the critical aspects of this strategy:
- Proximity to Suppliers and Manufacturers
One of the primary considerations when selecting a warehouse location is its proximity to your suppliers and manufacturers. Being close to your suppliers can reduce lead times, lower transportation costs, and ensure a steady flow of inventory.
- Access to Transportation Networks
An efficient warehouse must be well-connected to transportation networks. This includes highways, railways, ports, and airports. Easy access to these networks can expedite the movement of goods, reducing shipping costs and transit times.
- Customer Proximity
For businesses with direct-to-consumer models, being close to your customers is paramount. A strategically located warehouse can facilitate faster and cost-effective last-mile delivery, enhancing customer satisfaction.
- Cost Considerations
Warehouse location also impacts costs. Some areas may have higher real estate expenses or labor costs. Balancing these factors is crucial to maintaining profitability.
Evaluating Potential Warehouse Locations
Now that we understand the significance of warehouse location, let’s explore how to evaluate potential sites effectively:
- Conduct a Cost-Benefit Analysis
Before finalizing a location, conduct a comprehensive cost-benefit analysis. Calculate all expenses, from leasing or purchasing costs to ongoing operational expenses. Weigh these against the expected benefits in terms of efficiency and customer service.
- Consider Local Regulations
Different locations may have various regulations that can impact your warehousing operations. Ensure you are compliant with zoning laws, environmental regulations, and obtain any necessary permits.
- Analyze Labor Availability
Evaluate the local labor market for availability and skill levels. A location with a skilled and stable workforce can contribute to smoother operations.
- Assess Infrastructure and Technology
Modern warehousing often relies on technology and automation. Assess the local infrastructure for connectivity and the availability of technology partners.
FAQs
Can I change my warehouse’s location after it’s established?
Yes, it’s possible but often costly and disruptive. It’s crucial to choose the right location from the beginning.
Is it always better to be close to customers?
Not necessarily. It depends on your business model. For some, being close to suppliers might be more critical.
What’s the ideal distance from a transportation hub?
There’s no one-size-fits-all answer. It depends on your specific needs and transportation modes.
How can I estimate the ROI of a warehouse location?
Consider all costs and benefits over a reasonable time frame. A detailed cost-benefit analysis is essential.
Are there any tax benefits associated with certain locations?
Yes, some regions offer tax incentives to attract businesses. Investigate these possibilities during your location search.
How can I mitigate risks associated with local regulations?
Consult with legal experts familiar with the region’s regulations to ensure compliance and minimize risks.
Conclusion
Finding the sweet spot for your warehouse is a pivotal decision that can make or break your supply chain. By carefully considering factors like proximity to suppliers, transportation networks, customer locations, and costs, you can optimize your supply chain through your warehouse’s location for maximum efficiency. Remember, it’s a long-term investment, so choose wisely.
Incorporate these insights into your decision-making process, and you’ll be well on your way to ensuring that your warehouse becomes a strategic asset rather than a logistical hurdle.